
In modern industrial production, every step of the process requires the pursuit of ultimate efficiency. When it comes to the packaging of wet wipes or similar products, what kind of changes can an efficient filling and sealing machine bring to the enterprise.
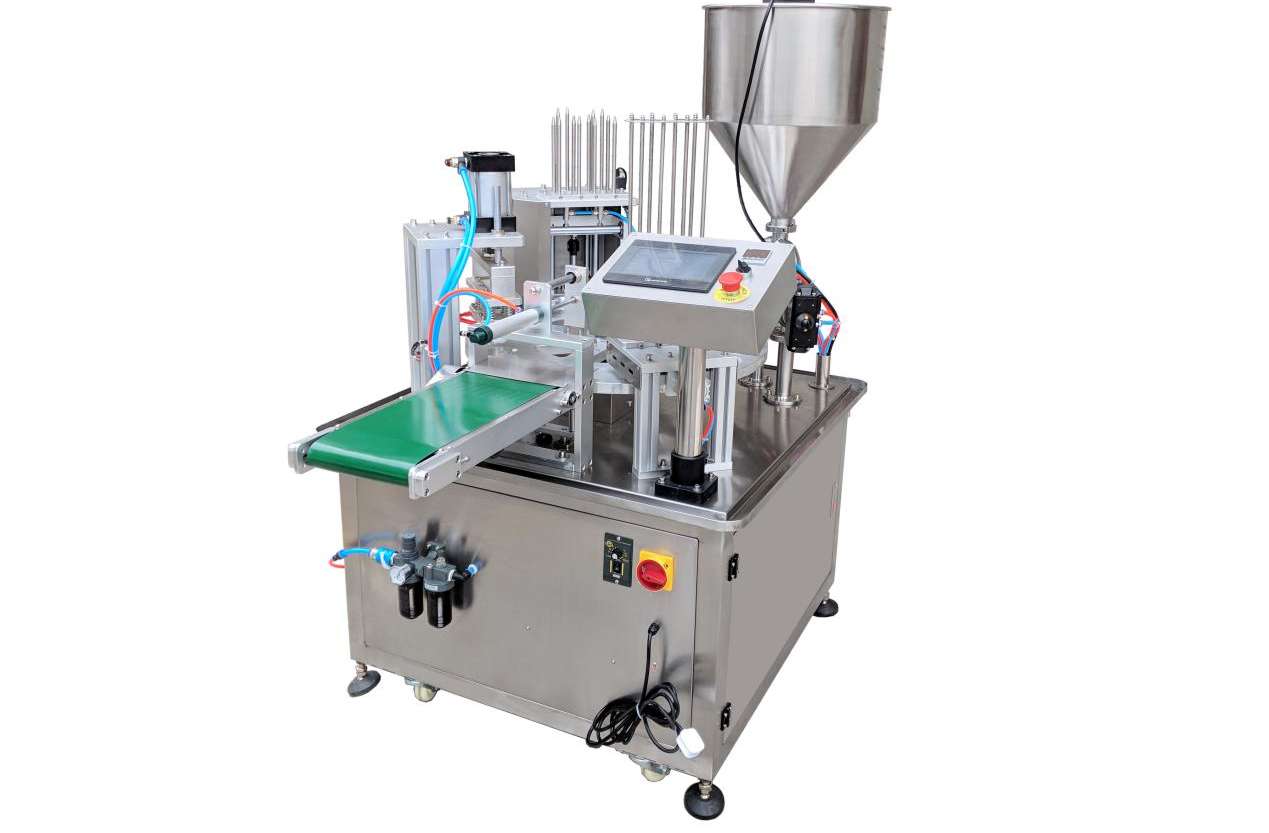
As an integrated production equipment that combines advanced technology, it can simultaneously complete the two steps of precise quantitative filling and firm sealing of wet towels. Compared with the traditional manual operation mode, this automatic process can not only greatly reduce human error, but also make the whole production line more smooth and compact.
For those who want to reduce costs without losing quality, this equipment is undoubtedly an ideal choice. Its high degree of automation means less time consumption and lower labor input-employees only need to start the device and monitor the running status, and the rest of the tedious work is done by the machine.
So what are the key technologies behind such excellent performance? First of all, it is worth mentioning the accurate sensing system, which can monitor the liquid level change in real time to ensure that every filling is just right; secondly, the high-speed rotating hot pressing module is used to quickly weld PE film or other material lids to form a tightly closed environment.
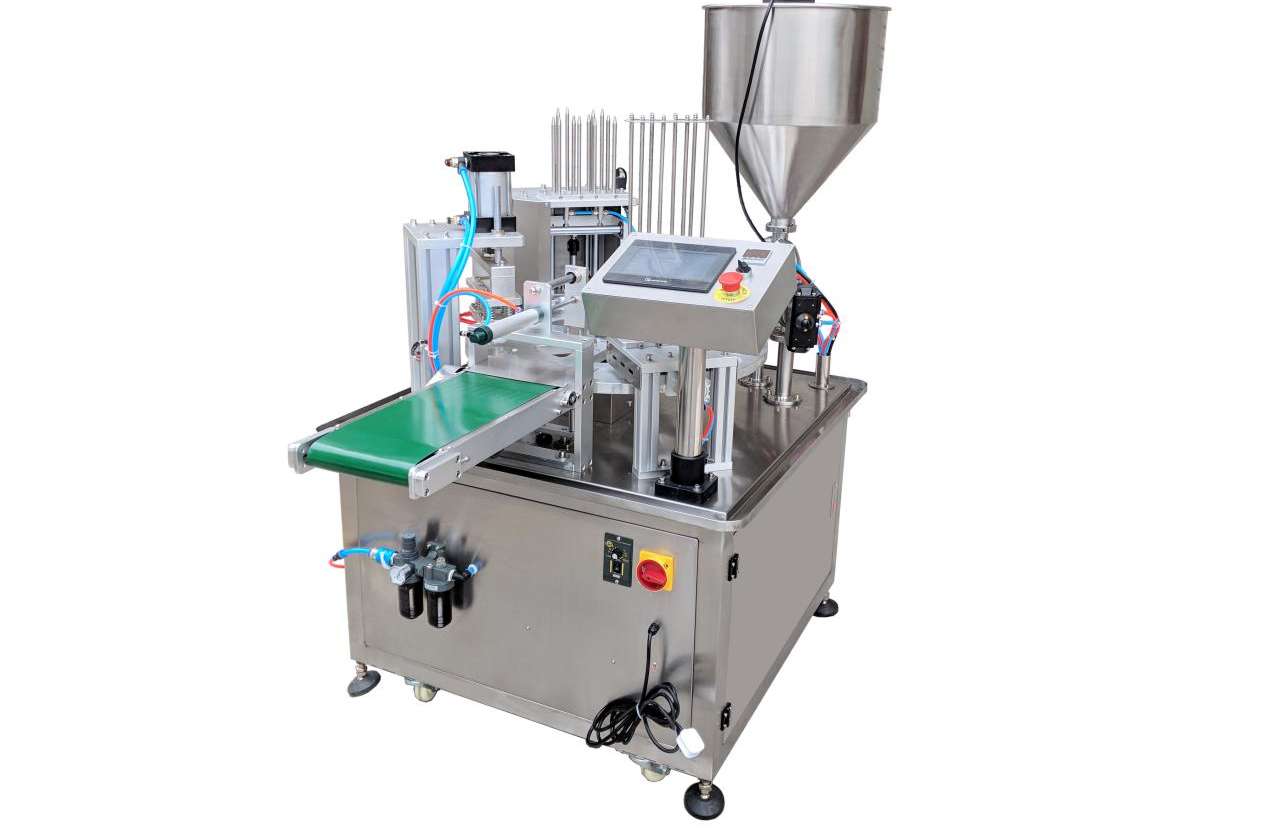
To better demonstrate its usefulness, here's a quote from Mr. Zhang, the head of a well-known sanitary product manufacturer: "Since the introduction of this new set of equipment, our daily output has increased by nearly 30 percent! And because of the reduced fatigue associated with repetitive work, workers also generally report that they work a lot easier than before." Such a successful experience undoubtedly provides a valuable reference for potential buyers.
of course, in addition to standardized services, this model also supports customized adjustments for specific customer needs, such as changing the capacity range or adding functional modules such as special pattern printing, which can be flexibly used according to the actual situation. Therefore, whether you are a small workshop or a large factory, you can find the version model that best suits your business development.
Although it has many advantages, proper maintenance is also a link that cannot be ignored. It is recommended to regularly clean the residual substances at key parts such as nozzles to prevent blockage, and check whether there is aging phenomenon in each connecting line, and replace the parts in time to avoid accidental shutdown.
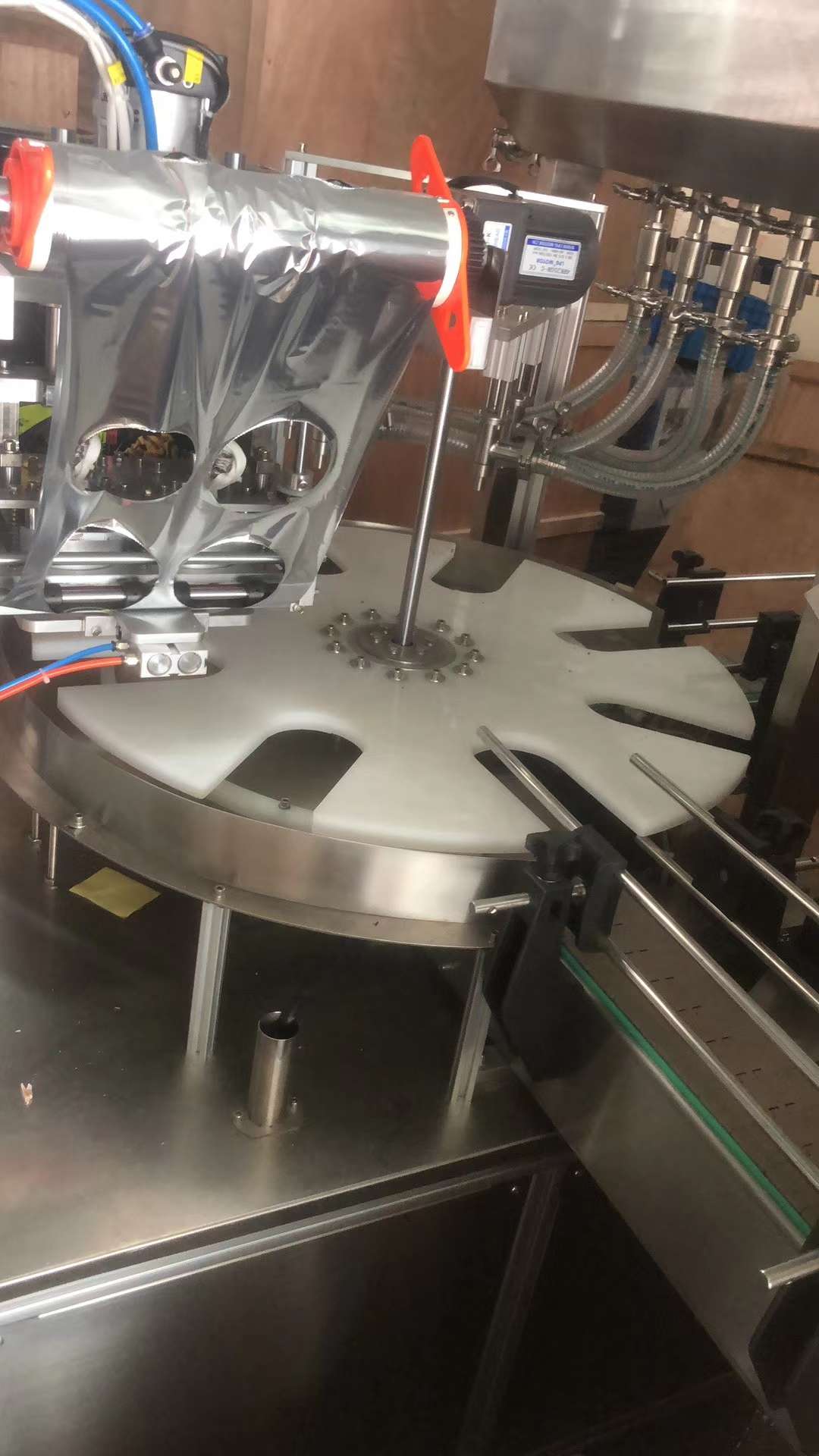
Finally, back to the original question-should we consider purchasing such high-end machinery? The answer is obvious: in the long run, this expense will translate into a significant return on investment. Because with the growing market demand and the rising trend of labor prices, having a set of stable, reliable and easy to manage processing tools has become the key to win the competitive initiative.
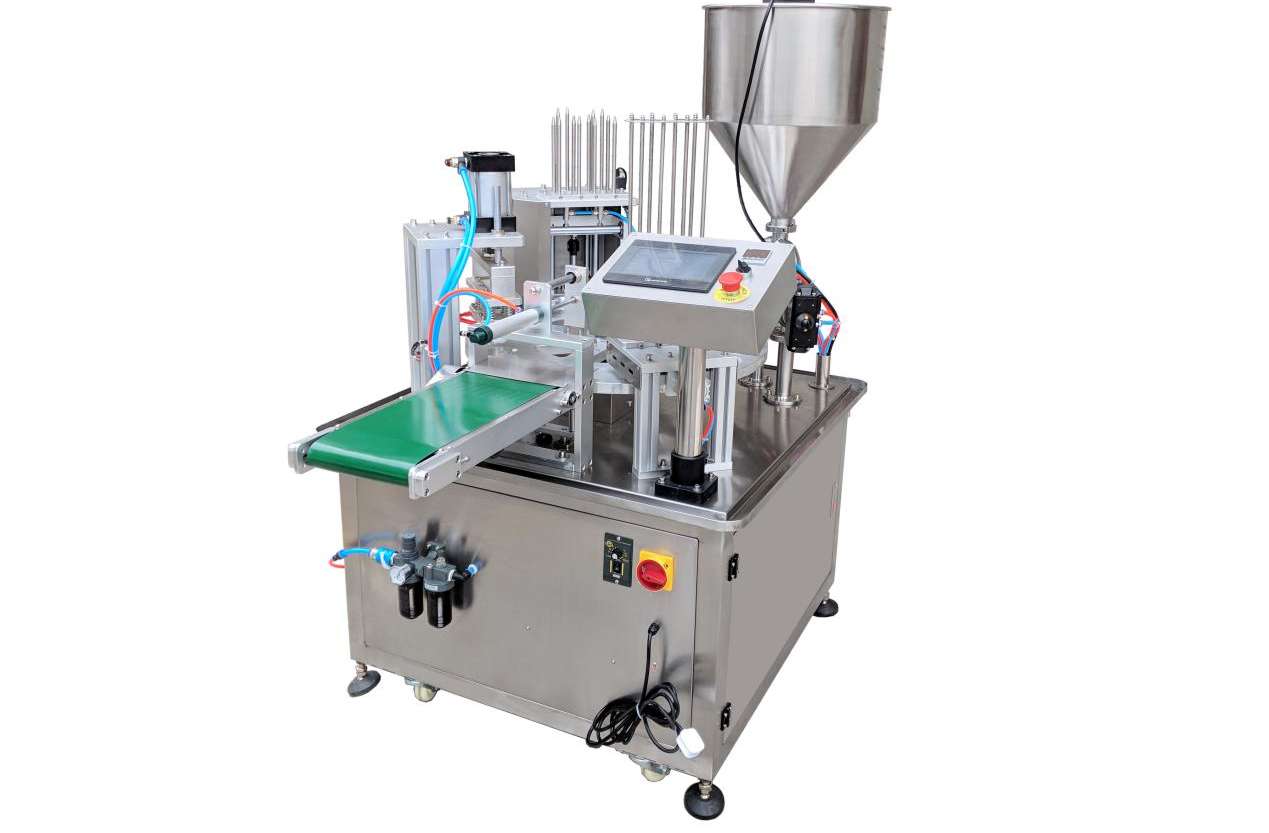